段付きシャフトの加工におけるポイント
段付きシャフトは、一般的な円筒形のシャフトとは異なり、
用途に応じて段差が設けられたシャフトです。
この段差によって、トルクや負荷を効果的に分散することができ、
用途としては主に自動車のエンジンやギア、モーターなどの部品に活用されています。
本記事では、段付きシャフトの特徴や、加工における当社の特徴、
実際の加工事例についてご紹介します。
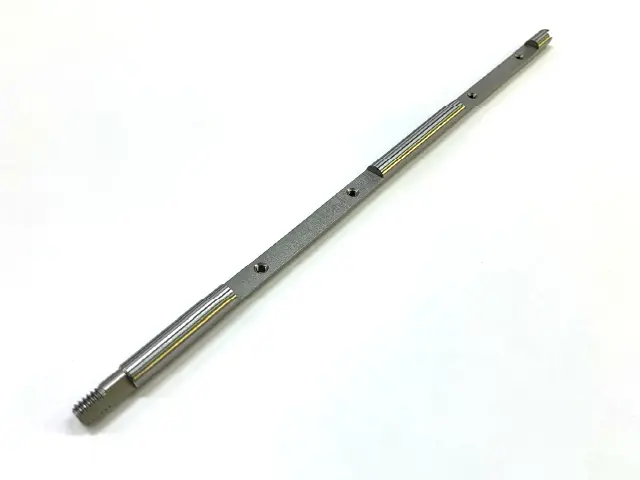
段付きシャフトの特徴
強度と剛性のバランスの最適化
段付き構造にすることで、特定の箇所に荷重やトルクが集中するのを防ぎ、必要な部分に強度を持たせ、
耐摩耗性や疲労強度を向上することができるため、最適な剛性バランスを実現できます。
取り付け精度の向上
段付きシャフトの特徴の一つとして、ベアリングやギア、プーリーなどの部品を正確な位置に取り付けやすいという
点があります。
通常の円筒形シャフトでは、ベアリングやギアを固定する際に、スナップリングやキー溝などを用いる
必要がありますが、段付きシャフトでは径が異なる段差があるため、部品を所定の位置に収める設計が可能です。
当社の段付きシャフトの加工のポイント
加工工程の分割
通常段付きシャフトを複合旋盤で加工すると8分かかるところを当社は、加工工程を分割することで
大幅に加工時間を短縮しております。
具体的には、段付きシャフトのDカット部分やHカット、Iカットなどをブローチ加工で仕上げることで
加工時間を短縮することが可能です。
また、仕上げの研削工程でインフィードの研削盤で2個取りすることでサイクルタイムも短縮することが可能です。
自動インライン検査による精度保証
当社では、位相精度やねじ精度を、工程間で自動インライン検査を実施することで高い精度を維持・保証しています。
具体的には、切かけ、スリ割り、2面幅、転造ねじ、多箇所内径ネジなどの複雑な段付き加工を工程ごとに分割し、
最短のサイクルタイムで生産できるラインを確立しています。
加工方法の最適化
ブローチ加工において、切削抵抗を少なくすることでバリの発生を最小限に抑え、材料の応力解放による曲がりを
抑制しています。また、多軸ヘッドで同時に4つのタッピング加工を行い、孔位置の精度を保証しています。
当社の段付きシャフト加工事例のご紹介
段付きシャフト
こちらは、自動車部品で使用される段付きシャフトです。従来、複合旋盤を用いた加工では8分を要していましたが、
工程を分割しライン化することで、わずか15秒で完了できるようになりました。
まず、中央部のDカット2か所の加工では、通常のエンドミルを使用すると80秒かかるところを、
ブローチ加工を採用することで、1ストロークで仕上げ、15秒で完了させています。
同様に、両端のHカットやIカットの加工も、エンドミルを用いると100秒を要するところを、
ブローチ加工によって15秒に短縮しました。
さらに、4か所あるタップ加工は、インデックス方式の専用機を活用することで、同時に加工できるようになり、
効率が飛躍的に向上しています。仕上げ工程においても、インフィード研削盤を使用し、2個取り加工を行うことで、
サイクルタイムを従来の半分に削減しました。
段付きシャフトの加工は特注シャフト・スリーブ加工.comにお任せください!
いかがでしたでしょうか。
特注シャフト・スリーブ加工.comを運営する協和製作所では、段付き加工のみならずあらゆる材質、形状のシャフトの
加工に対応しております。
また、高い生産技術力と生産ラインの自動化により量産品を短納期で納めることができます。
シャフトの加工でお困りの方はお気軽にご連絡ください。